Amidst the stunning backdrop of the Firth of Forth, Lothian’s dedicated team at their coachwork facility at Seafield is hard at work, repairing and restoring Lothian’s vehicles to the incredible high standards the people of Edinburgh and the Lothians expect.
A true ‘hidden gem’ of the business, Seafield is home to a team of 22 talented colleagues, including Spray Painters, Coachbuilders, General Assistants, a Store Manager, a Trimmer and even a Tinsmith. There are also five apprentices learning their trade among the vastly experienced team, and they’re in good hands under the guidance of Steven Tait, Bodyshop Supervisor at Seafield.
The team manage repairs, repaints and refurbishments of Lothian’s vehicles. Each different discipline at Seafield has its own station within the building where you can find tradesmen hard at work.
Away from the hustle and bustle of the main workshop, Seafield’s Spray Painters are repainting panels on Lothian’s vehicles, freshening up their look and returning them to service looking as good as new. Before being painted, buses are meticulously covered section-by-section to protect the parts not needing worked on.
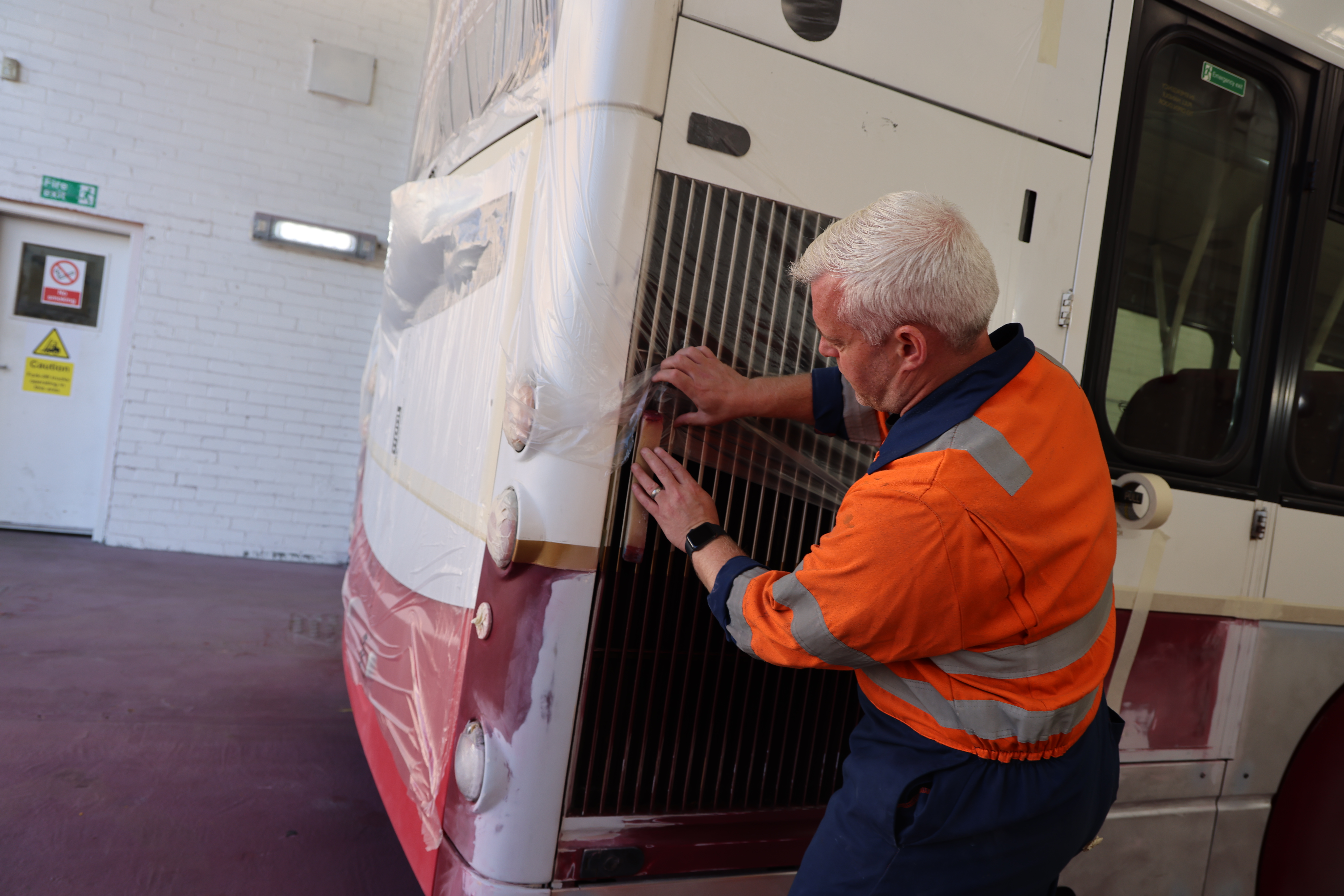
“The covering part of the job is really important,” says Mark Robertson, one of the Spray Painters at Lothian.
“This way, we can paint each section separately, giving the whole bus a real crisp, professional look once it’s done.
“Anyone can paint but not everyone can prep,” he adds. “It’s definitely an art!”
Painting Lothian’s famous madder and white buses is no mean feat. The dedicated team at Seafield work hard over even the smallest detail. It can take up to a full day to paint a bus from start to finish, such is the precision that the team must work with.
Further inside Seafield, Coachbuilders are seen replacing steel panels on Lothian vehicles. Every vehicle that enters Seafield is inspected thoroughly before any repair is carried out. Panels that have seen better days are marked for replacement.
From there, metal sheets are placed through Lothian’s new ‘Press Brake’ machine, which is a piece of high-tech machinery that cuts and bends the metal sheets for the panels for Lothian’s vehicles.
Each of the intricate specifications for every type of vehicle Lothian operates is loaded into the machine’s database, and after a few button presses, metal sheets are cut to those dimensions. This means even more of the repair work carried out on Lothian vehicles can be done in-house, ensuring vehicles are back in service sooner.
“People would be surprised at just how much we do here at Seafield,” says Shaun Kenneally, one of Lothian’s Coachbuilders.
“We do everything that we can ourselves, and to a high standard.”
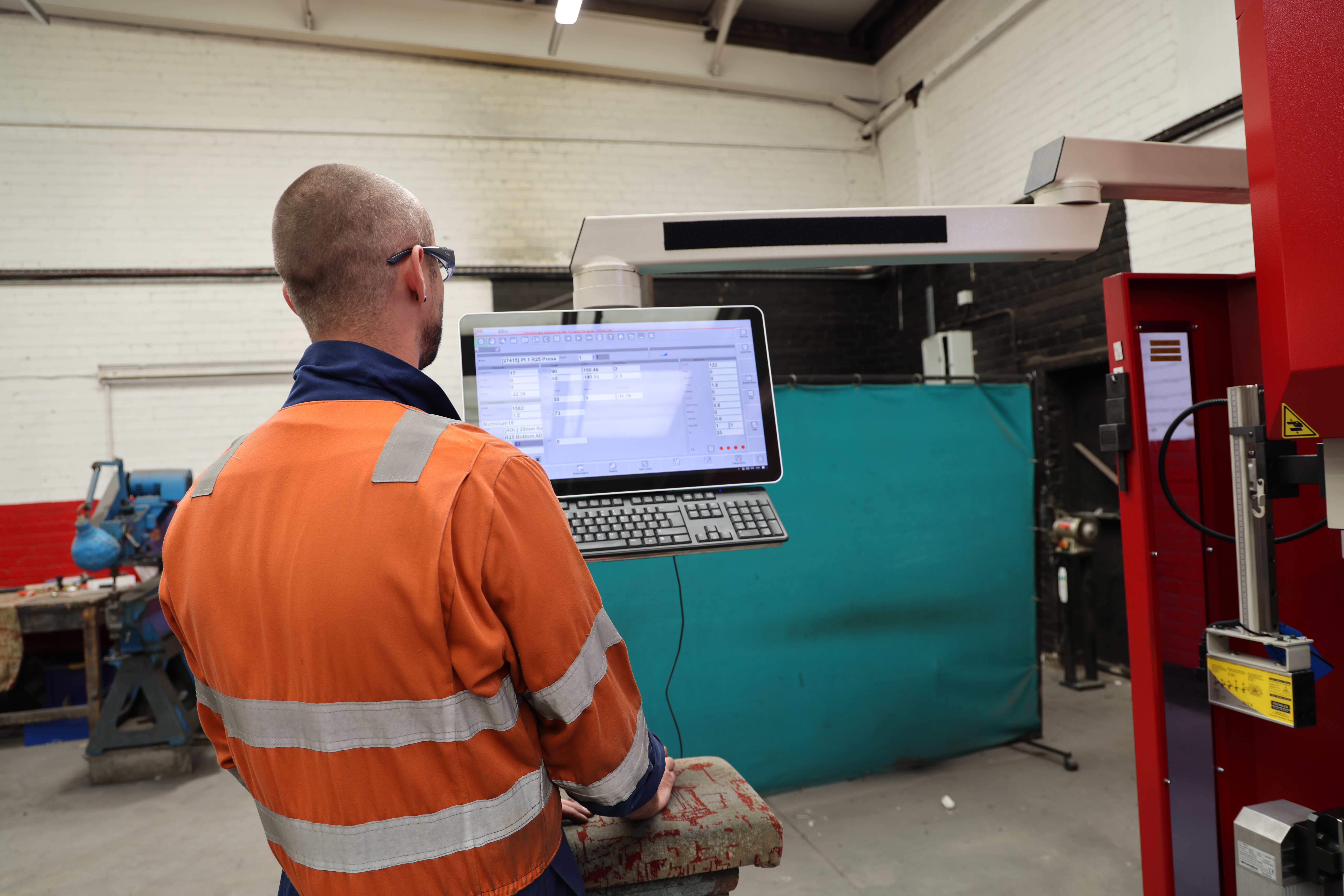
It’s an incredible effort from the team at Seafield on a daily basis. It’s not all high-tech either. There’s still plenty of scope for the tried and tested practices that have become a staple at Lothian for decades.
Lothian’s vehicles are known for their interior design, specifically the seats. The material (known as the moquette) which covers each seat on every bus is cut by hand by a dedicated trimmer at Seafield. In a quieter part of the building, huge rolls of felt are marked and cut before being wrapped around cushion pads, which are neatly piled up and labelled for each specific garage across Lothian’s business.
On the main floor, colleagues are at hard at work repairing buses. Although to the untrained eye some damage may look irreparable, there is no panic among the team at Seafield.
Professionalism shines through across the whole facility. This is a hard-working, high performing team which takes its responsibility extremely seriously.
“It’s a really good group of people here,” says Stevie Tait. “They come in each and every day and get to work. They’re all knowledgeable and determined to do a good job every time.
“Among our team are some really experienced colleagues who have been here for their whole careers, more or less.”
Health and Safety is adhered to without exception. You can’t look anywhere in Seafield without seeing health and safety advice. The team take the utmost care for themselves, as well as the buses they’re working on.
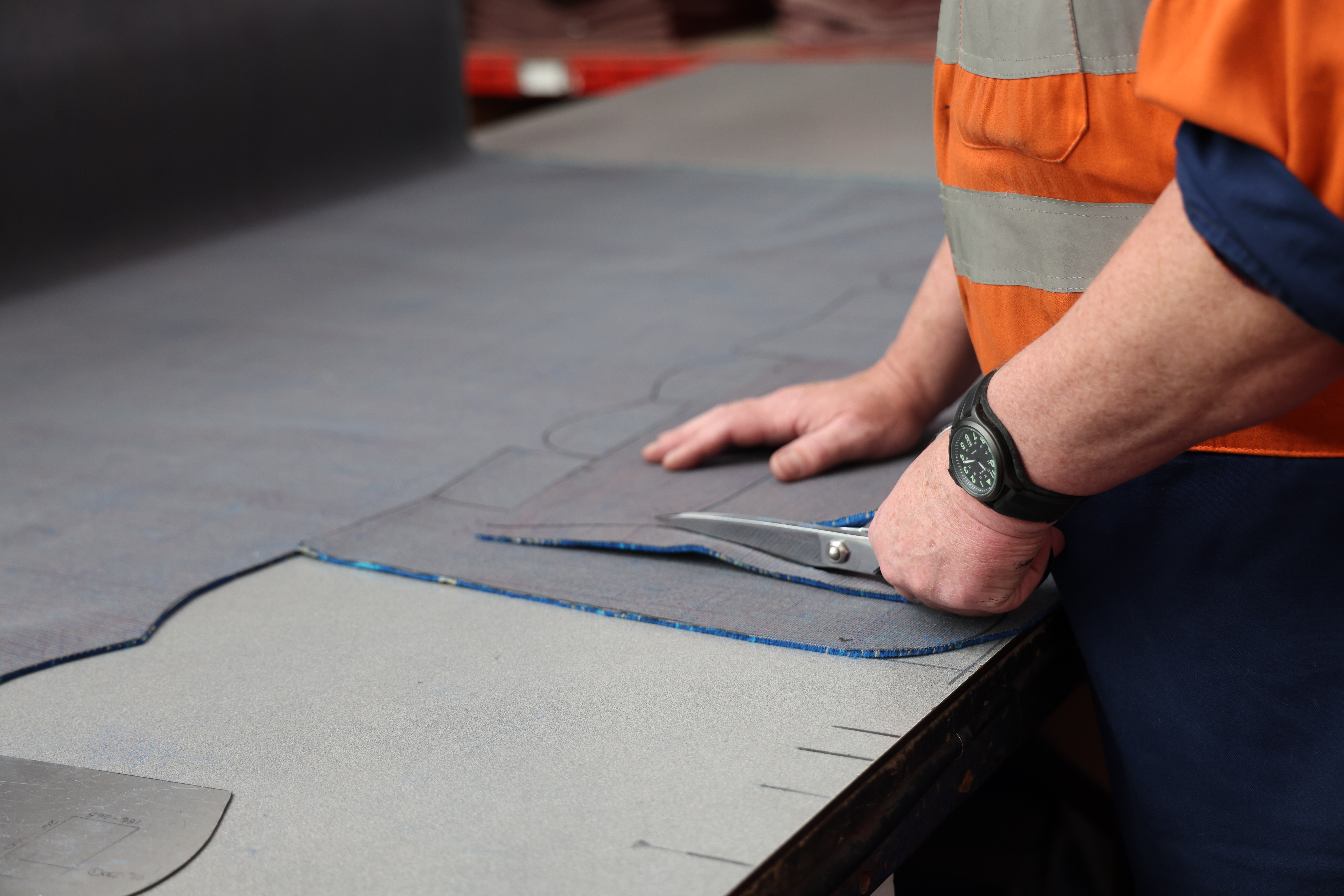
Among the team at Seafield are Apprentice Coachbuilders, embarking on their career journey at the business. As coachbuilding is a unique area of Lothian’s operation, its exciting to see these individuals paired up with some of the most experienced and skilled engineers in a challenging yet understanding and engaging environment.
Jensen Falconer, a third year Apprentice here at Seafield, has begun learning the process of spray-painting vehicles with Mark. He believes this will help him become a better all-round engineer in the future.
“It’s great for me to develop my skillset further,” says Jensen. “It means that if the team is short or other areas are busier than others, I can help out and continue to contribute in the workshop.”
Lothian is known throughout the industry and beyond for the extremely high standards of their vehicles, which is only possible thanks to the high standards established and demanded from the teams across the business.
Seafield is a just another example of these high standards. Working collaboratively with Lothian’s three other operational engineering garages to ensure your bus is safe, reliable and turned out in an exceptional condition.
So, if you were ever wondering what the secret is behind Lothian’s vehicles always looking their best, now you know the answer; a lot of hard work and ingenuity from our dedicated team at Seafield.